The Drill Down, Issue #10: Dynamic Positioning Systems
Introduction
As the offshore oil and gas industry pushed exploration into deeper water, it found that conventional anchoring became less practical and cost effective. The advent of Dynamic Positioning (DP) was the answer to the need for a more robust method of remaining in a single location for a prolonged period of time without the use of anchors. DP offered an effective, yet complex solution to remaining stationary while conducting high consequence operations. In this Drill Down, the basics of a DP system will be discussed.
What is Dynamic Positioning?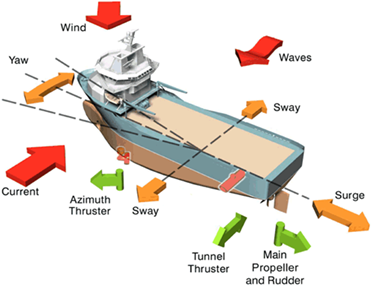
A DP System is a computer-based control system used to automatically maintain a vessel’s heading and position without the use of mooring lines and/or anchors. Horizontal movement of the vessel is controlled on 3 separate axes (image right):
- Surge (fore and aft)
- Sway (side-to-side)
- Yaw (heading)
System computers receive input from various sensors to determine the external forces being applied to the vessel. This information is then processed to determine the amount and direction of force that must be applied by the vessel in order to maintain the required position and heading. Thrusters then execute the commands given from the system and exert the desired force.
A vessel’s DP system utilizes 7 onboard elements in order to control horizontal movement of the vessel:
- Position Reference Systems
- Environmental & Motion Sensors
- Power System
- DP Controller
- Thrusters/Propulsion System
- Human-Machine Interface
- Human Element (DP Operator)
A depiction of the 7 elements is shown below:
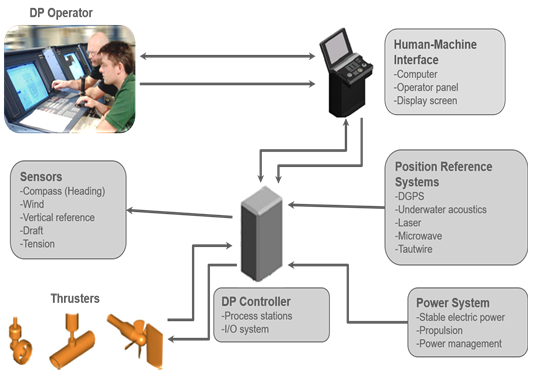
1. Position Reference Systems
In order for the DP system to keep a vessel in a desired position, it must utilize a Position Reference System (PRS). The PRS identifies the vessel’s current location (known as “taking a fix”) and compares it to the desired location. There are a variety of methods utilizing either absolute or relative position, including:
- Satellite (DGPS, DGNSS),
- Underwater Acoustics (HPR),
- Laser (Cyscan®, Fanbeam®),
- Microwave (Radascan®), and
- Tautwire.
2. Environmental & Motion Sensors
- Motion sensors measure the other 3 axes of movement: Pitch (fore and aft rocking), Roll (side to side rocking) and Heave (up and down movement). The DP system cannot control these movements, but they must be accounted for in order to correct PRS fixes.
- Wind sensors - Input from wind sensors are needed for measuring wind speed and direction. This information is used to account for external forces affecting horizontal movement of the vessel.
- Compass (Heading) - The gyrocompass constantly provides the DP System with the vessel’s current heading data in order to correct PRS fixes.
- Tension Sensors - Vessels, such as pipe laying vessels, generally use tension meters to provide the DP System with data regarding the tension forces of the weight of the cable or pipe pulling on the vessel during laying operations in order to better determine external forces affecting horizontal movement of t
3. Power System
The Power System is an arrangement of mechanical and electrical equipment that provides power to the Thruster/Propulsion system in order to maintain position. The power system is often part of an automated power management system designed to ensure adequate and reserve power is available.
4. DP Controller
The DP Controller computer is the “brain” of the DP system: receiving input data, processing, and outputting commands. The controller is loaded with a reference model in order to execute this. Simply put, pre-loaded vessel characteristics are compared against the vessel’s actual behavior with its environment. The model corrects for any discrepancies between expected and actual behavior and updates itself, continually improving accuracy. The model is then able to predict how measured external forces will affect the vessel’s ability to maintain position, and react accordingly.
There is an assortment of forces acting on the vessel that cannot be measured. These forces are summed up into one value knows as “measured current.” Measured current is the calculated difference between the measured forces’ effect on the vessel’s position and force (thrust) applied to counteract the measured forces. This value is used by the DP controller to constantly apply the corrected force and direction to maintain location and improve the DP model. The model workflow can be seen in the image to the right (source: Wikipedia).
5. Thrusters
Thruster/Propulsion systems are arranged to provide adequate thrust for maneuverability and maintaining position. Depending on the vessel type, this system could be a combination of main propellers and rudders, azimuth thrusters, tunnel thrusters, and drop-down thrusters. While power for thrust is provided by the Power System, the DP Controller calculates the required thrust.
6. Human-Machine Interface
The DP control station displays information from the Power, Thruster and DP Controller systems necessary to operate and monitor the DP system. Here the operator is capable of commanding the DP system, monitoring for alarms, as well as manually controlling thrusters if necessary.
7. DP Operator
The DP Operator is the human element of the DP system. He or she inputs the desired course/heading/location in the system and monitors the system’s ability to execute the desired command.
Conclusion
Dynamic Positioning has revolutionized vessel station keeping capabilities, allowing vessels to operate within feet of desired positions for prolonged periods of time. Albeit a complex system, the employment of DP has been a significant benefit to vessels conducting high consequence operations on the outer continental shelf.